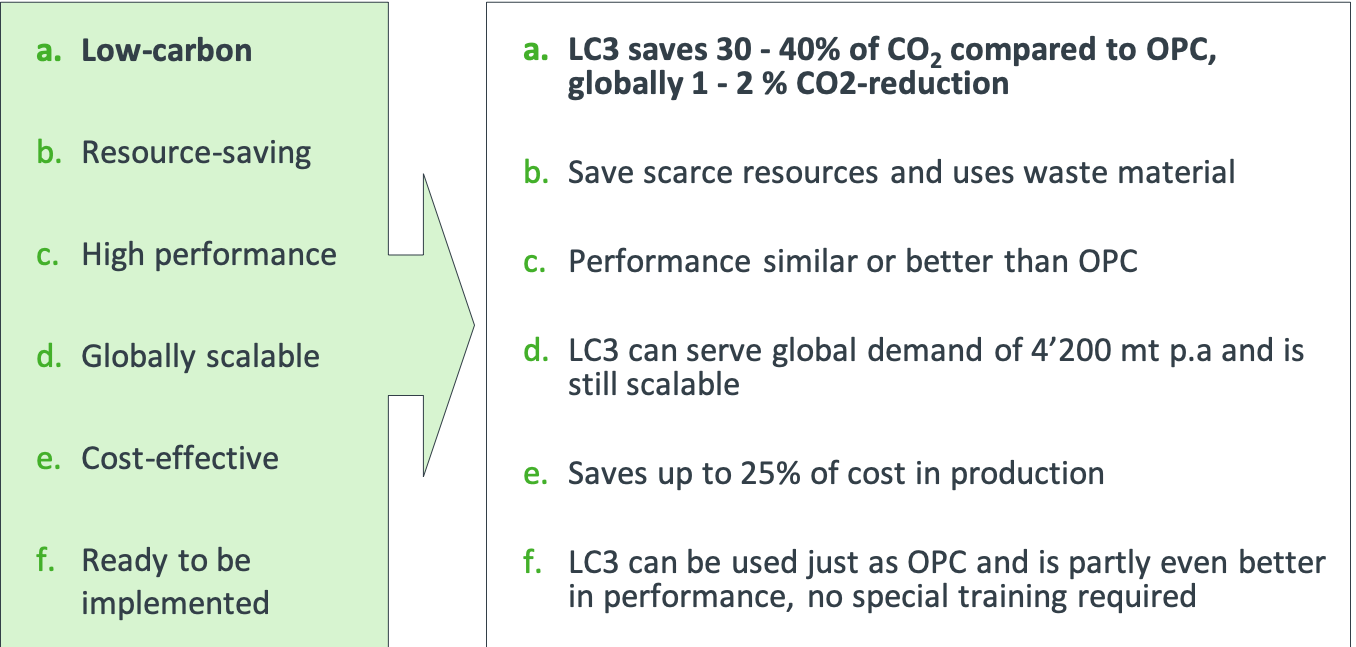
a. CO2-savings
LC3 saves up to 40% of CO2 as compared to Ordinary Portland Cement.
Most of the CO2 comes from the clinkerisation process. Therefore, reducing the clinker factor and replacing it with SCMs is the fastest intervention to save high numbers of CO2.
Within the clinker production, there are two main sources of CO2. Firstly, clinker needs to be burnt at very high temperatures between 1400 and 1500°C. Secondly, CO2 embodied in limestone is released during production. Reducing the clinker content therefore means to save both energy-related and emobied CO2.
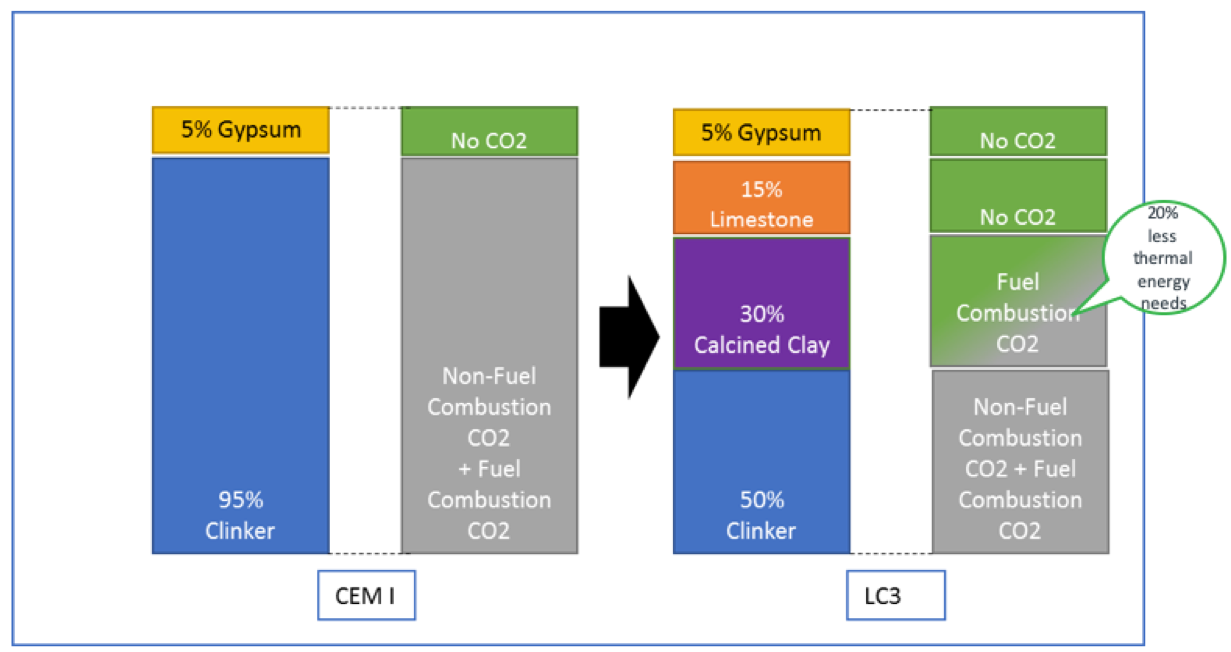
b. Resource-savings
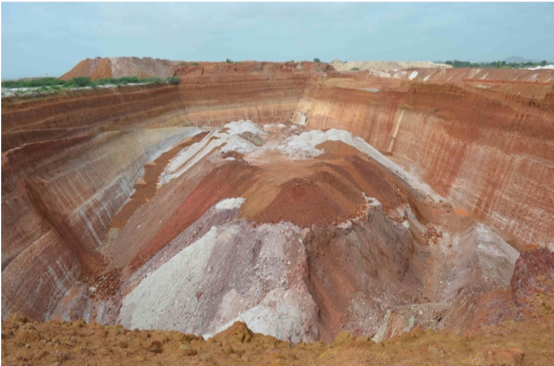
- Clay waste e.g. ceramic or cosmetic industry
- Less purity of limestone required, e.g. dolomite presence
- Low prices for the raw materials
- Avoiding creating waste
Avoiding cost (e.g. for landfill taxes)
c. High performance
For more than 10 years, the prestigious research institutes EPFL, IIT Delhi and Madras and CIDEM have test LC3 in all different aspects and came to the result LC3 reaches OPC - CEM I performance.
Not only in lab conditions but also through industrial trials and applications these findings were confirmed. They are constantly monitored in existing LC3-applications in different parts of the world and environments (e.g. marine or high-altitude applications).
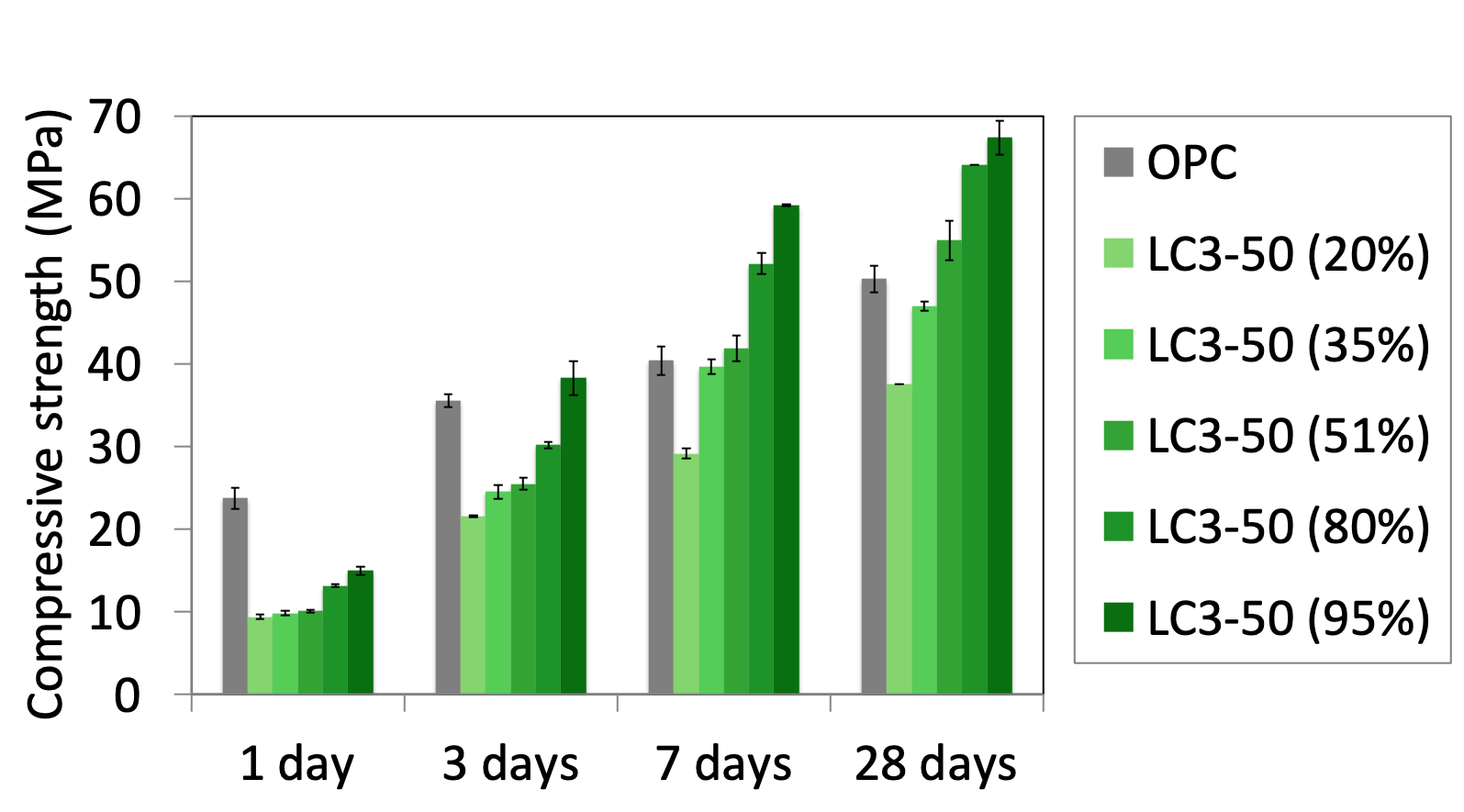
d. Globally scalable
The raw materials limestone and calcined clay are abundantly available worldwide.
Other commonly used Supplementary Cementitious Materials like fly ash or slag are already fully used and cannot be scaled for the use in cement. Furthermore, with increasing focus on sustainability more and more coal power and steel production plants are expected to be closed. This will further cut the supply of these materials as SCMs.
The only material largely available and in sufficient quantity are kaolinitic clays.
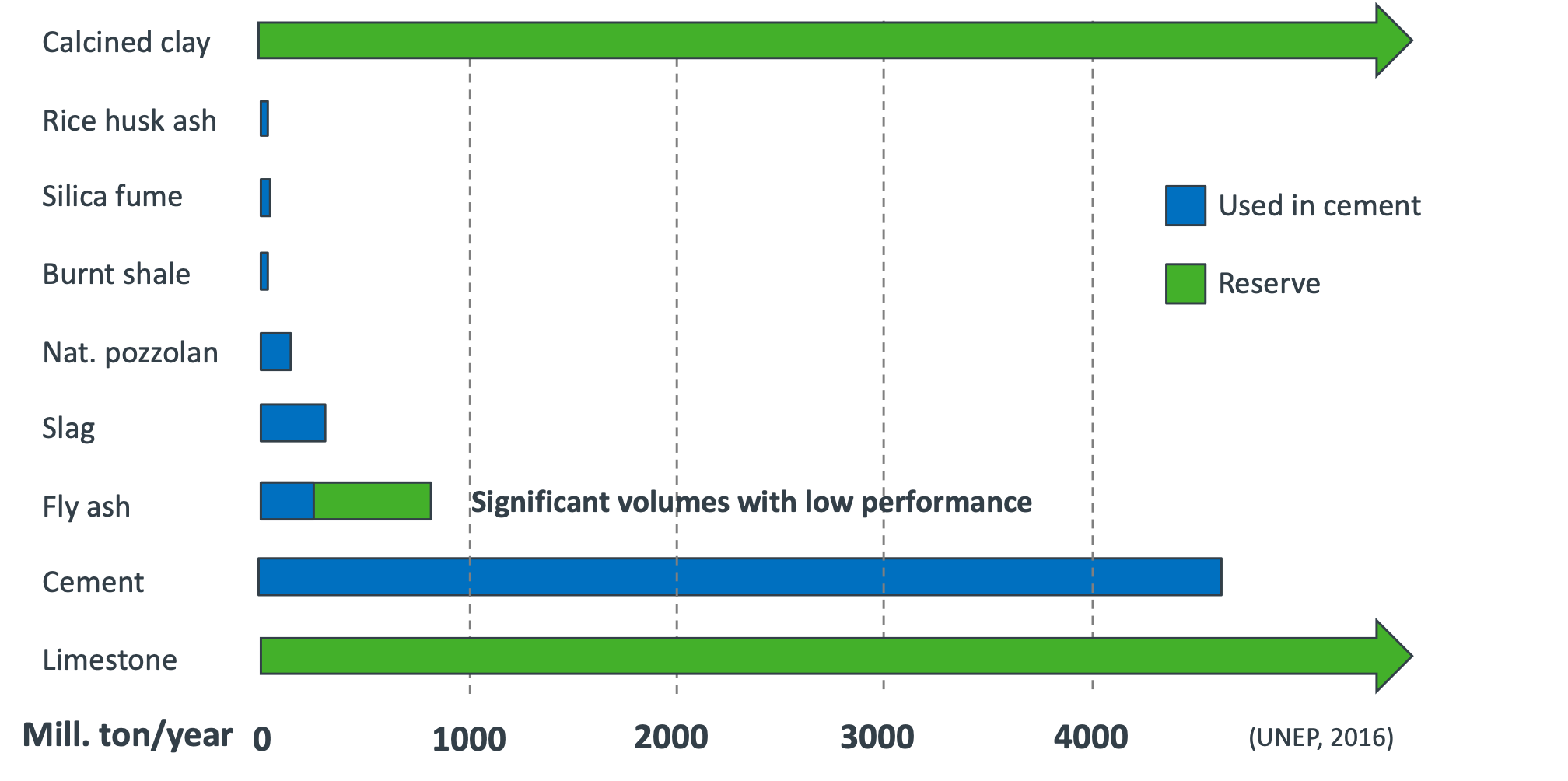
e. Cost-effective
Different scenarios of producing LC3 were analysed financially in a study by the cement market experts Cementis. Their results showed that with a cement plant, grinding plant or Greenfield scenario the production of LC3 is profitable. The main indicator for driving the profitability is the close access to suitable clays.
Overall, the production cost can be up to 25% lower for LC3 than for OPC due to savings for energy and material. This is without additional policy incentives, such as green funds or carbon certificates, which can further increase the attractiveness for cement producers.
a
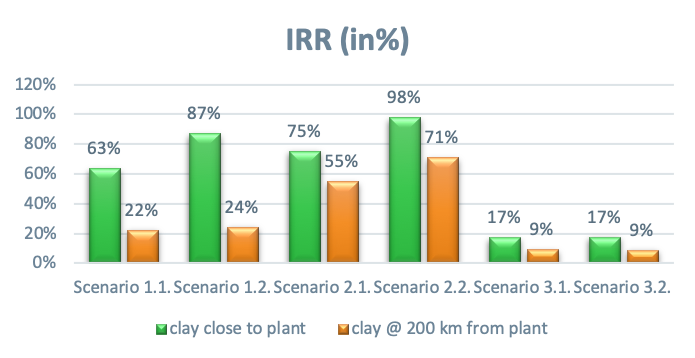
f. Ready to be implemented
LC3 is a technology which is market-ready and it is already produced in several plants in the world. The sooner the technology is rolled out globally the more CO2-emissions can be avoided.
The already existing readiness of the technology for the industrial uptake is an important distinction compared to other green technologies.
Furthermore, LC3 can be used without additional training by builders. In India, demo constructions were built without further providing training.
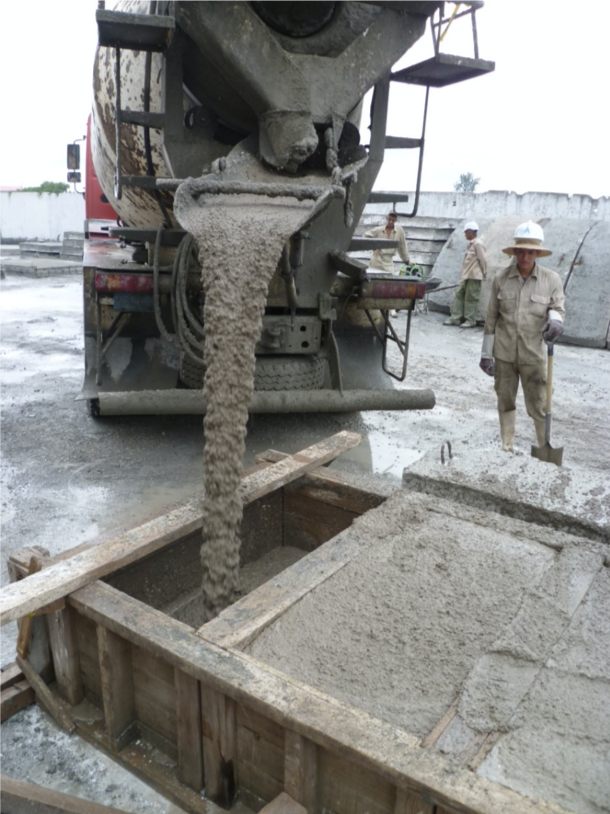