The ambition towards implementation of ‘low-carbon’ concrete in the industry is evident nowadays. Nevertheless, there is certain ambiguity observed in the approach of manufacturers, specifiers and wider industry regarding the adoption of sustainable concrete. Fragkoulis Kanavaris of Arup and Karen Scrivener of EPFL identify part of the ambiguity that can adversely impact the actual implementation of environmentally friendly concretes in the industry.
There is no clear definition of what low-carbon
or sustainable concrete means and such terms
have been inconsistently used by designers,
specifiers, manufacturers, contractors,
technology developers and researchers.
The predominance of concrete as a construction material and its perception as having a high carbon footprint have long been recognised by the concrete industry and wider engineering community. Due to the above, there is a need to develop and use realistic concrete solutions in construction that are environmentally friendly. Different approaches for developing, defining, specifying and using ‘low-carbon’ concretes have been observed in the industry with varying degrees of success and efficiency. This potentially occurs due to lack of consistency and understanding of relevant processes across the value chain. In this article, we address certain issues that are thought to inhibit a wider adoption of actual environmentally friendly concretes.
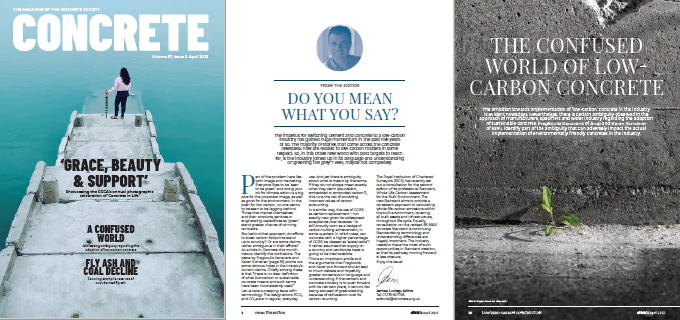
THE PROBLEM OF PERCEPTION
Generally, concrete can be frequently perceived as a planet-threatening man-made construction material. While this may be partially true due to the sheer volumes of concrete used for construction purposes globally, by comparison with other currently available construction materials concrete encompasses the lowest carbon footprint per unit weight of material used. Furthermore, concrete is often the preferred material for construction due to its versatility, durability and robustness. Therefore, it is not concrete as a material per se that encompasses these risks for the environment, but the sheer volume of the global demand for it for construction purposes. Reducing the volume of concrete produced and used would be a more appropriate approach to carbon reduction in the concrete construction industry. However, since construction of infrastructure is required as part of demographic development, there is an urgent need to find solutions towards carbon reduction in concrete.
While it is recognised that, where possible, the use of concrete should be minimised, it should be noted that there is no other material that can replace concrete to any significant extent. To put this into context with an example, replacing only 25% of the demand for concrete on a global scale with timber would require a new forest 1.5 times the size of India and waiting over two decades for the trees to grow.
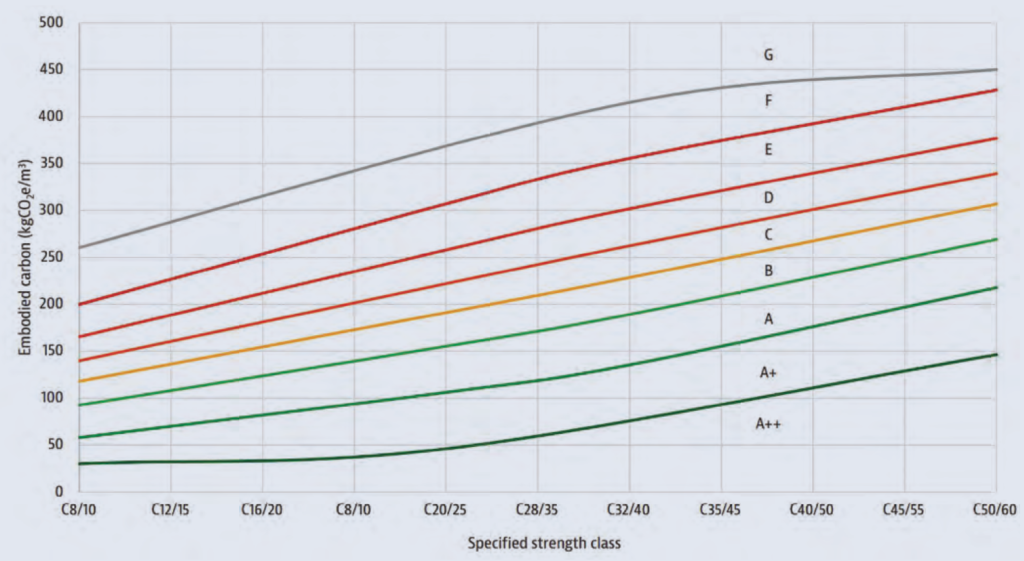
THE PROBLEM OF DEFINITION
The terms ‘low-carbon’ ‘lower- carbon’ and ‘sustainable’ concrete emerged over the past decade and have extensively been (mis) used in the industry over the past five years or so. However, there is no clear definition of what low- carbon or sustainable concrete means and such terms have been inconsistently used by designers, specifiers, manufacturers, contractors, technology developers and researchers. In fact, there can probably be no globally applicable definition of lower/low-carbon concrete as the embodied carbon of concrete depends on location, type and application, industry experience, material availability and construction needs. Commendable efforts by working groups in the UK, such as the Low Carbon Concrete Group (LCCG), to produce a concrete embodied-carbon classification tool and inform a potential definition are shown as an example in the graph above. While this has been a good starting point, it also revealed limitations of such classification approaches to account for complexities associated with:
- concrete compositions used in different applications, eg, piling, pumpable, cast in-situ, precast, prestressed/post-tensioned concrete, lightweight, heavyweight etc;
- necessary adaptations in concretes according to weather, casting and exposure conditions;
- concrete mix data collection and bias, and how the data can affect the ‘shape’ and numerical values of classification curves; and
- location of the project, eg, there are different concrete constituents and supplementary cementitious materials available in different parts of the UK and globally.
To the authors’ best understanding, ‘low-carbon’, ‘lower-carbon’ or ‘sustainable’ concrete is a concrete that encompasses a considerably lower carbon footprint compared with a best-practice or business- as-usual mix for a given application at a particular location and time, while exhibiting adequate durability and mechanical performance.
The term ‘lower-carbon’ concrete could be potentially used more consistently in the industry if employed in the comparison of two or more concretes. However, it is recognised that the industry might need to move away from these terms, as it appears they have been predominately used as branding mechanisms for best-practice or ‘innovative’ concretes with no unequivocal evidence of actual long-term carbon reduction.
THE PROBLEM OF AVAILABILITY OF MATERIALS
There are two main practical avenues adopted in the industry towards the reduction of embodied carbon of concrete:
- partially or totally replacing Portland cement clinker and
- optimisation of concrete mix proportions and reduction of binder content through enhanced particle packing and use of consistence-enhancing admixtures.
There is speculation that GGBS (slag), which has been used in concrete in England and predominantly in the Greater London area for many years, will not be available in the near future, due to high demand and reduced production; however, there are conflicting views from different parties within the industry. On this particular issue of GGBS availability and use in concrete, an IStructE–ConcreteZero task force has been formed in the UK and is working towards producing relevant guidance imminently. Regardless, it should be pointed out that GGBS should not be considered as a long- term solution for carbon reduction of concrete globally, as it could only replace less than 10% of the Portland cement produced worldwide. The suitability of clays in the UK for use in concrete after calcination requires information on the availability of clays in different regions and examination of their properties, which is the aim of an ongoing major EPSRC research project. Going forward, it is anticipated that in approximately two years, it might be possible to import calcined clay consistently from different parts of the world.
THE ROLE OF MANUFACTURERS
Cement and concrete manufacturers have a major influence on the environmental impact of the concrete that is produced and used in the industry. It is noted, however, that much of the ‘low-carbon concrete’ branded by manufacturers is largely based on GGBS in varying proportions within concrete. Since GGBS has been used for decades in concrete and given that it is a finite source of supplementary cementitious material, the approach of maximising GGBS addition towards achieving or claiming to achieve lower-carbon concrete is not deemed to be the most appropriate going forward. Equally, attention should be given to use GGBS efficiently when incorporated in alkali-activated materials, especially when these are using large quantities of GGBS and chemical activators. Providing the full picture on the actual concrete carbon-footprint reduction and composition is expected to aid the transition to a less carbon-intensive industry.
THE ROLE OF NOVEL TECHNOLOGY DEVELOPERS
There have been several novel technologies developed that aim to reduce the embodied carbon of concrete and, more generally, of cementitious products. It has been observed, however, that it is quite common for the novel technology developers to advertise their products/patents as an industry-disruptive technology that can dramatically reduce the carbon footprint of concrete globally through a pioneering process and essentially ‘solve the problem’ of carbon in concrete. However, this conveys the wrong message in the wider engineering community and public, as such technologies normally severely lack standardisation conformity, scalability and production capacity, comprehensive test data associated with concrete production and application, and actual trials on elements with monitoring in place.
Consequently, the term ‘novel’, when assigned to a concrete technology, has been associated not only with promising technologies, but also with those far from implementable. Acknowledging that most novel concrete technologies are based on sound and meritorious scientific efforts of varying degrees of maturity, it is recommended that technology developers be more transparent with respect to the properties and potential limitations of their technologies, while understanding construction needs and expectations. One of the possibilities to achieve that is through interdisciplinary collaboration with designers and contractors.
THE ROLE OF SPECIFIERS/DESIGNERS
Designers are those who conduct the design of a concrete structure and for most cases in the UK specify certain requirements for the concrete in terms of its composition. It is normally not expected that structural engineers/designers have a comprehensive understanding of concrete materials specification and how that could be efficiently conducted. Appropriate concrete specification requires understanding of the availability of materials in a particular region and the potentially adverse effects of alternative/secondary concrete constituents in its performance related to an intended application. As such, designers and structural engineers should be aware of specification implications or consult materials specialists during the early stages of the design, eg, avoiding: over-specifying 28- day strengths, specifying secondary/recycled aggregates in locations where these need to be transported from far away with relevance to the project location, over-specifying GGBS and including more supplementary cementitious materials in concrete specifications. From a design perspective, ensuring that sections are not overdesigned is crucial, with respect to avoid using more concrete than necessary.
THE ROLE OF CONTRACTORS
Contractors are those who actually build designed structures and infrastructure, and encompass significant capacity to embrace alternative concrete technologies and even conduct trials and tests as part of a project. It has been observed that in most cases, decisions on materials are predominately cost- and time-driven, which often excludes the consideration of alternative or carbon-efficient technologies. In addition, contractors should engage more with designers and manufacturers in an interdisciplinary manner towards delivering concrete solutions with a reduced carbon footprint. This is to capture potential complications in structural/material behaviour of the considered concrete, as well as explore opportunities with regards to monitoring, which can be used to enhance understanding of the performance of non-conventional concretes.
CONCLUDING REMARKS
Developing, specifying, producing and using ‘low-carbon’ concrete is of ever-increasing importance for the construction industry and for the planet. However, the term ‘low-carbon’ concrete, or similar, has been used inconsistently within the industry, even for concretes and technologies that are not lower in carbon compared to best-practice/business-as-usual concretes, that are not efficient long-term solutions, or that are far from industry readiness. This is something that can deter the reflection of what is actually happening in the industry, with respect to reducing the embodied carbon of concrete. Delivering environmentally friendly concrete solutions requires a solid understanding of current practices, the availability of materials and sources of carbon in concrete, as well as avoiding greenwashing. Stakeholders in industry and academia have a role to play towards reducing the embodied carbon of concrete and interdisciplinary collaboration is required to achieve an optimum solution for a project and derive a feasible path towards concrete decarbonisation.