Construction is underway on the 85-meter Tilia Tower near Lausanne: the first large-scale building in Switzerland to be built with a low-carbon cement developed in EPFL’s Lab of Construction Materials.
Construction consortium Induni-Maulini broke ground on the Tilia Tower this spring, and the project is expected to finish in 2026. The building will span 27 floors and include 221 rental apartments, plus nearly 4,000 square meters dedicated to dining, co-working, and well-being. In addition to its modern architecture and emphasis on mobility, the project prides itself on its prioritization of a reduced carbon footprint.
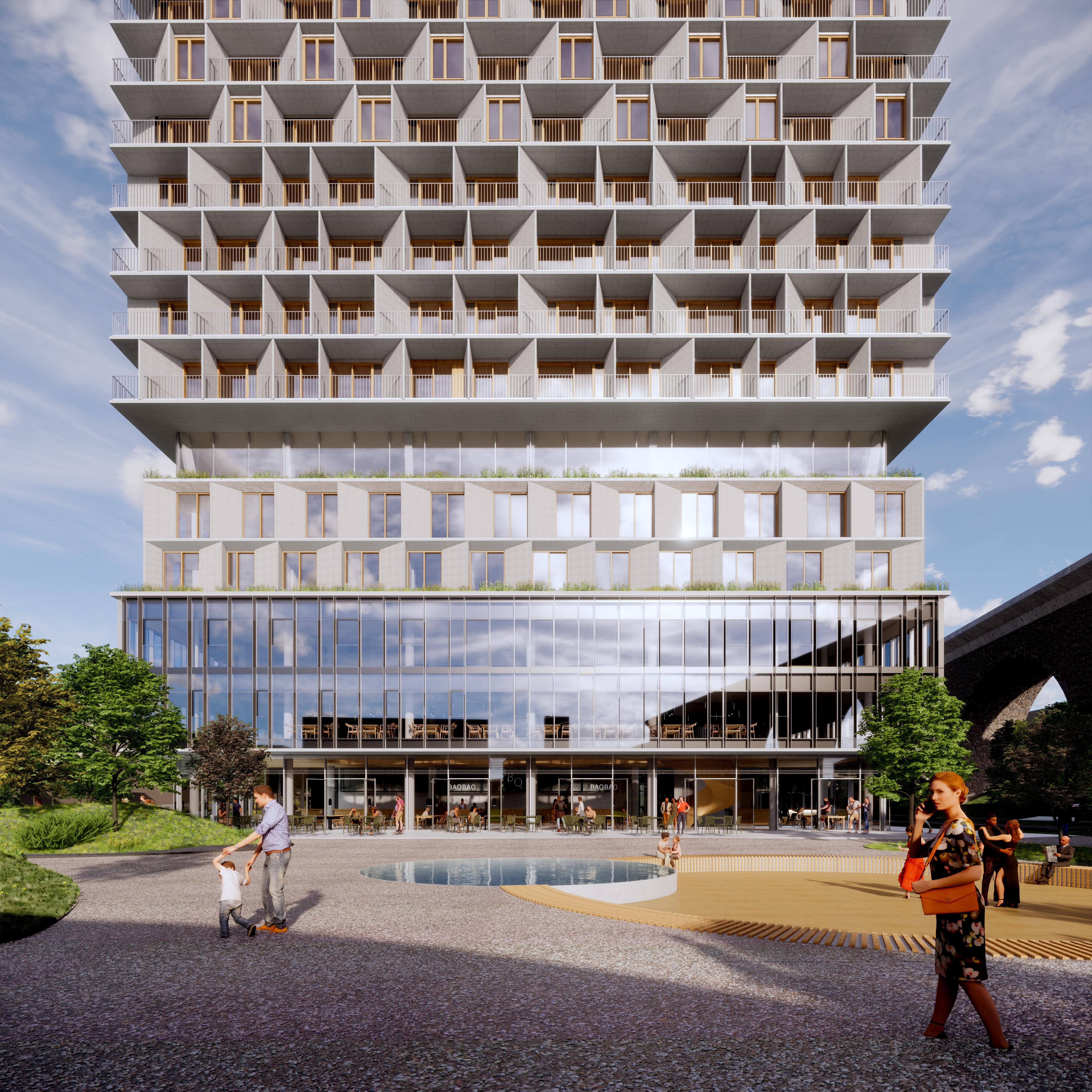
One way the project aims to meet its low-carbon pledge is through the use of LC3 (Limestone Calcined Clay Cement). Developed by Karen Scrivener, head of the Construction Materials Laboratory (LMC) in EPFL’s School of Engineering, LC3 replaces a large part of the carbon-intensive clinker with limestone and calcined clay, reducing CO2 emissions from production by up to 40% compared to traditional cement.
The project bears witness to the excellence of EPFL research, and its contribution to sustainability in the construction of what will be the tallest of four high-rise buildings in Malley.Beatrice Malchiodi, EPFL LMC
“Tilia Tower provides a showcase for the performance and viability of LC3 just 10 minutes from the campus where it was developed. The project bears witness to the excellence of EPFL research, and its contribution to sustainability in the construction of what will be the tallest of four high-rise buildings in Malley, in the district of Lausanne,” says LMC postdoctoral researcher Beatrice Malchiodi.
The Tilia Tower’s proximity to the campus offers the LC3 research team valuable opportunities to closely observe the material’s behavior on a large scale, and receive direct feedback from Induni-Maulini engineers on its application. “We can for instance identify critical aspects that need to be further researched or developed in the lab, to facilitate a faster adoption of LC3 in the construction sector,” Malchiodi adds.
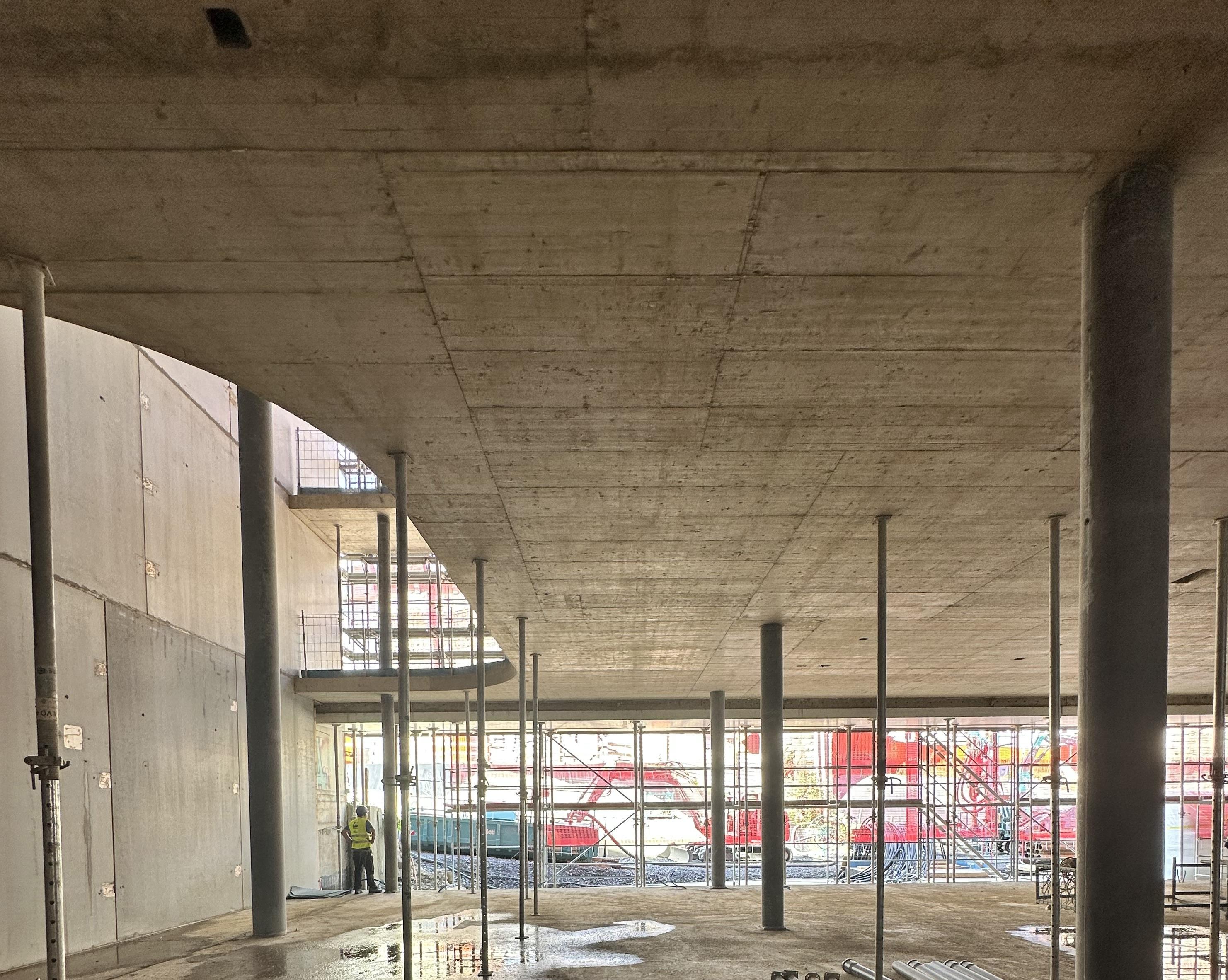
Equivalent – or superior – quality
LC3 has already been used in construction in India and Latin America, but this is the first building in Europe to integrate the material, which will comprise about one-third of all cement used in the project. The construction team is using an LC3 variety called Jura Eco 3: an ecobau and Minergie-ECO-certified cement containing clay mined in the Swiss Jura mountains, and calcined to become reactive.
The LC3 cement Jura Eco 3 is designed to offer high strength and durability, while complying with the most stringent quality standards.Julien Blot, Induni-Maulini
Induni-Maulini engineer Julien Blot says their experience using the product has been “very positive.”
“The LC3 cement Jura Eco 3 is designed to offer high strength and durability, while complying with the most stringent quality standards. It offers a quality equivalent, if not superior, to that of traditional cements,” he says.
The tower’s underground structure has already been built with LC3 cement, which is also being used for above-ground walls, slabs, and supports. Thanks to its warmer color compared to traditional concrete, it can also be integrated into floor coverings and exposed architectural elements.
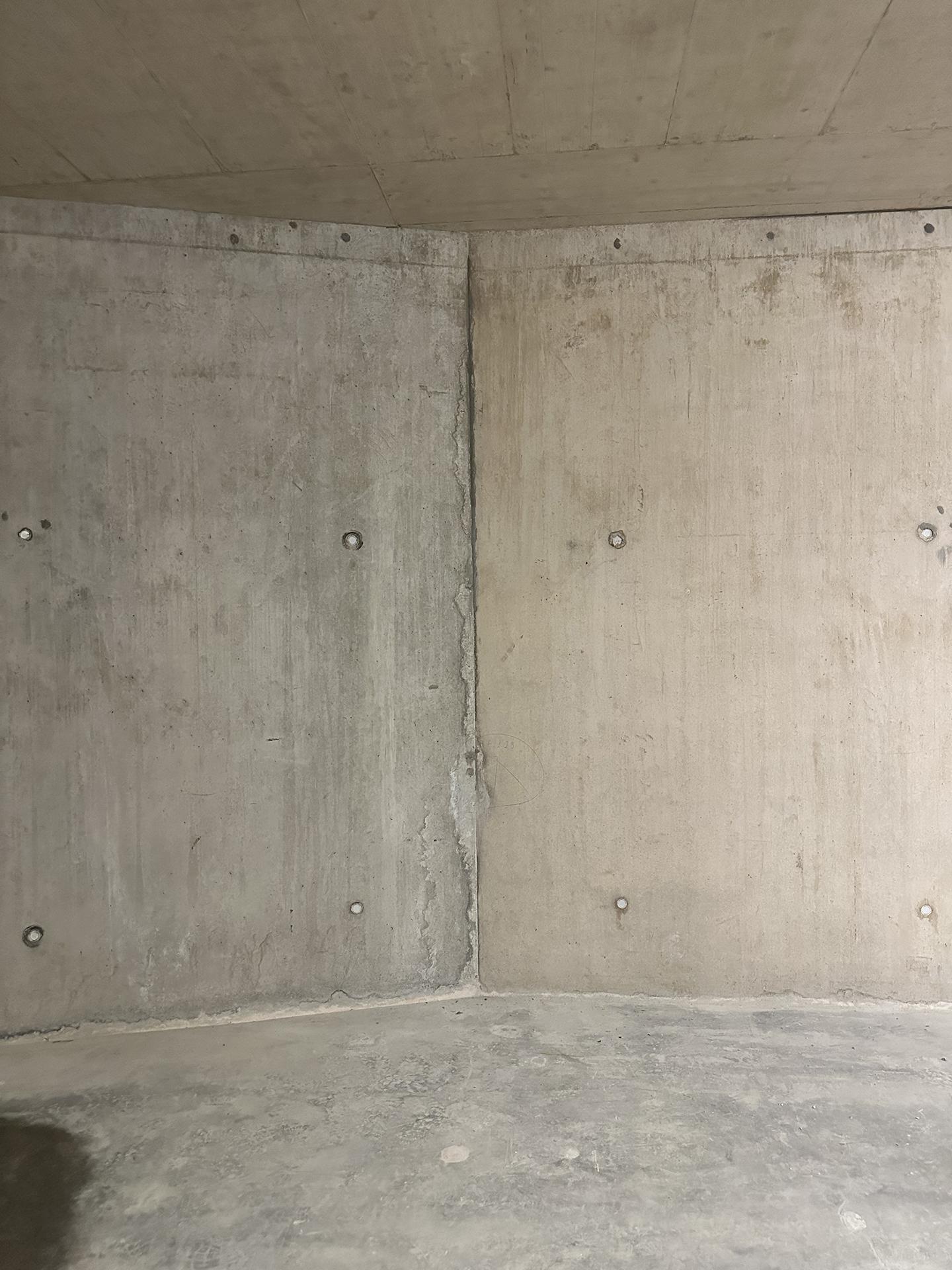
“Although its color is slightly different due to its environmentally friendly components, it pours, shapes, and hardens in a similar way to ordinary concrete, making it easy to use on building sites. However, it is important to take this color difference into account, to ensure a consistent and satisfying aesthetic for customers,” Blot says.
He adds that having EPFL’s LC3 researchers close by is also of great benefit to the construction team.
“EPFL helps us understand the product better, and their team makes useful recommendations to us on how to improve our methods when applying LC3.”
Investing in the future
Due to its composition and properties, which are similar to those of traditional cement, LC3 can be integrated into construction projects without requiring major modifications to conventional building techniques. However, concrete produced with LC3 cement usually comes at a small additional cost – around 3% for Jura Eco 3, for example. This is due to investments in research and development, as well as to the fact that the current production of low-carbon cement is not yet at the scale of conventional cement.
Nevertheless, Blot sees a strong future for low-carbon cement in the construction industry.
“This low extra cost is offset by the long-term benefits in terms of sustainability and lower environmental impact, making LC3 a cost-effective choice over the life of the project,” he says. “Moreover, we anticipate that eco-concrete will continue to develop thanks to the growing emphasis on sustainability in the construction industry. Technological advances and increased demand will foster its widespread adoption, while collaborations between industry players will encourage innovation and integration into standard practices.”
Author: Celia Luterbacher
Source: Materials Science and Engineering
This content is distributed under a Creative Commons CC BY-SA 4.0 license. You may freely reproduce the text, videos and images it contains, provided that you indicate the author’s name and place no restrictions on the subsequent use of the content. If you would like to reproduce an illustration that does not contain the CC BY-SA notice, you must obtain approval from the author.