A new material developed at EPFL could change how we make cement forever — and cut 500 million tons of emissions by 2030.
Under the stewardship of Karen Scrivener, head of EPFL’s Laboratory of Construction Materials at the School of Engineering, a team of researchers has been wrestling with the environmental implications of concrete, a material produced at an astonishing four tonnes annually for every human on Earth. The challenge? Cement, concrete’s binding component, accounts for a significant 8% of worldwide emissions. And clinker, the key component in cement, is extremely carbon intensive, making up 90% of overall cement emissions in the fabrication of concrete. The solution? LC3, short for Limestone Calcined Clay Cement. Not just an alternative, LC3 offers the potential for enhanced durability, cost-efficiency, and a significant reduction in emissions. Finding a solution to reduce the climate impacts of concrete while providing for the needs of growing economies is vital.
LC3: the innovation changing the cement industry
LC3 addresses both sources of carbon emissions from making clinker. First, it replaces half of the clinker with calcined clay and ground limestone, neither of which release carbon when heated the way limestone does. Second, the clay is heated to a much lower temperature, which reduces the amount of fuel required and resulting emissions. With lower temperatures it is also more feasible to switch to cleaner energy sources such as electricity than it is for making clinker. LC3 can reduce CO2 emissions around 40% compared with conventional cement by replacing half of the clinker.
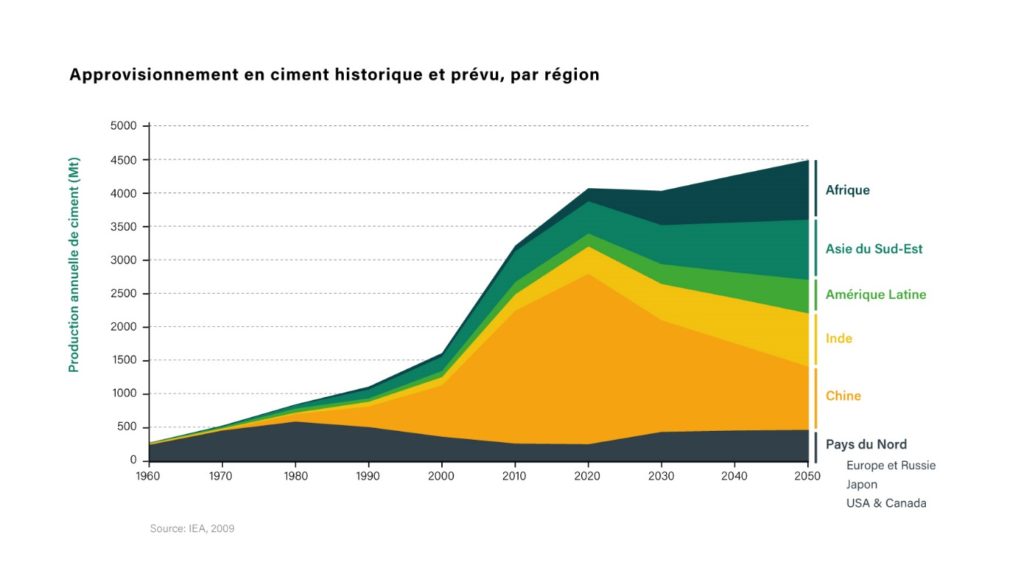
Data source: UNEP 2017 Ecoefficient cements report
LC3 is functional, too. It is less pervious to water and salt, so it makes concrete roads and bridges more durable and longer lasting, reducing the cost and disruption of replacement. Since it requires less energy to make and uses widely available clay it can be produced at a lower cost, up to 25% lower.
Cutting 500 million tons of CO2 by 2030
LC3 is already growing rapidly and is currently being produced in a number of plants around the world. For each ton of calcined clay produced, we are saving 600 kilograms of CO2. By the end of 2023 LC3 will have already saved around 15 million tons of CO2. By 2025 it is expected that LC3 will have saved 45 million tons. If the cement industry widely adopts the use of LC3, it can help prevent up to 500 million tons of CO2 emissions by 2030.
Many of the leading cement producers are in the process of adopting calcined clay cement. Holcim, for example, announced in January 2023 the launch of operations at a plant in France that will deliver up to 500,000 tons of low-carbon cement per year. Argos Cementos in Columbia produce 2.3 million tons of LC3 cement a year, which is already being used locally in the construction of roads, tunnels and buildings.
The future of cement in the Global South
In the coming years and decades, the majority of new construction worldwide will occur in the Global South — particularly in Africa, where the population is expected to increase by 1 billion by 2050. That means a lot of cement.
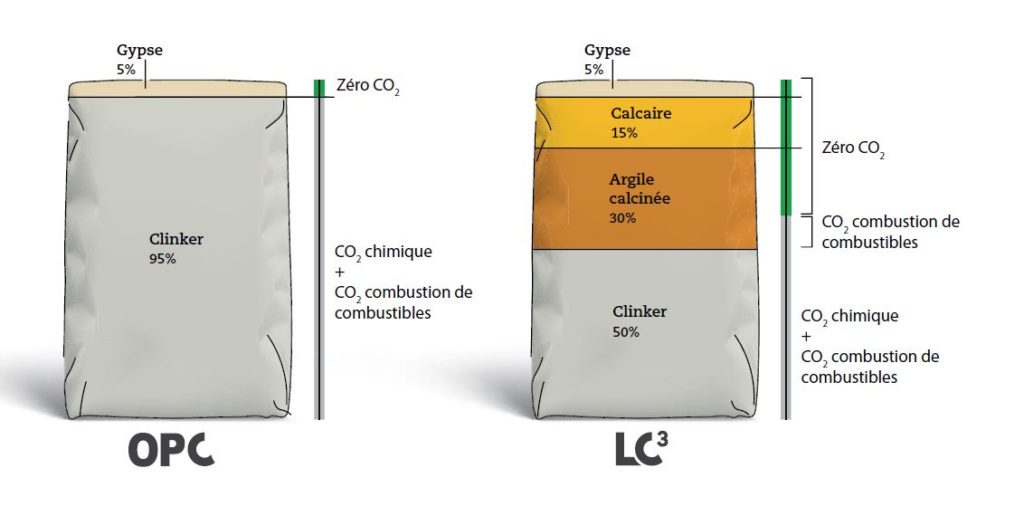
Data source: UNEP 2017 Ecoefficient cements report
Africa has the world’s fastest-growing population, yet suitable limestone to manufacture clinker is scarcely available on the continent. Today, the costly import of clinker has a direct impact on costs. It causes affordability issues for housing and infrastructure. Fortunately, clays are the weathering products of common rock types. As a result, they are widely available in most geological settings. Clays containing kaolinite, the most suitable clay types for LC3, are abundantly available across Africa.
By adopting LC3 technology and replacing a substantial part of clinker with local resources, African countries and those across the Global South can create world-class local industries and reap the economic and employment benefits. This will reduce the need to import clinker with foreign currency and allow the construction of housing and infrastructure at lower costs, all while limiting CO2 emissions.
A reimagined concrete value chain
Reducing the amount of clinker in cement reduces emissions in the production of cement, but there are many additional strategies if we look across the entire value chain of concrete. By improving the energy efficiency of plants and using alternative fuels such as waste fuels, we can further reduce CO2 from the production of clinker. By more carefully selecting the aggregate size gradations there is less void space for the cement paste to fill, saving on cement cost and emissions.
We can also improve the design and efficiency of concrete used in structures and buildings. The Global Cement and Concrete Association estimates that this could save 22% of concrete while also cutting costs. Finally, adapting certain design elements and increasing efficiency as well as recycling materials will further reduce the impact of concrete on the climate. If all of these strategies are combined, we can achieve up to 80% reduction in the emissions from cement and concrete using today’s technologies.
To reach this goal, stakeholders across the industry must work together, from the cement and concrete producers, contractors and trade partner, design team and owners. Changing existing practices and gaining momentum for an industry-wide shift requires diligence and perseverance. There needs to be strong willingness from both the private and public sectors to work together to facilitate a transition to net zero emissions in construction while providing solutions for sustainable growth. Now more than ever we need public-private cooperation to see real solutions scale.
Authors: Mediacom , Scott Shell, Jeremy Edward Packham, Karen Scrivener
Source: EPFL